HRSG Stack Welding
HRSG Stacks are subjected to accelerated corrosion where sulfur is present in the fuel (gas/oil). An engineered solution is to protect stack internals with a coating which contains glass flake. For the coating to adhere it must be applied on a properly prepared substrate (NACE/SSPC/Manufacturer’s Recommendations). Glass flake coatings cannot be effectively patched.
In this case, the stack field welds were not compliant with AWS D1.1, 5.24.4 (visual examination criteria), the construction contract criteria. This poor workmanship necessitated rework of the welds and stack coatings. Concerns include welder qualification, lack of weld inspection, lack of coatings prep inspection, and pervasiveness of defect (full length, all stacks). Additionally, the stack alignment lugs were not ground smooth in preparation for the coatings.
Another concern with unacceptable weld profiles in the stack is weld failure due to expansion and contraction of the stack during outage cycles and wind loads, especially in the presence of sulfur.
Blasting, weld repair, and recoating of one stack required a 2 month outage (each). There were 12 stacks total.
Minimal. It takes no more time to weld properly, but perhaps some minor labor savings was gained with an unqualified welder
Owner: 2 month outage, revenue loss at $35,000/day =~$2,000,000. EPCC: ~$400,000 to repair welds and recoat.
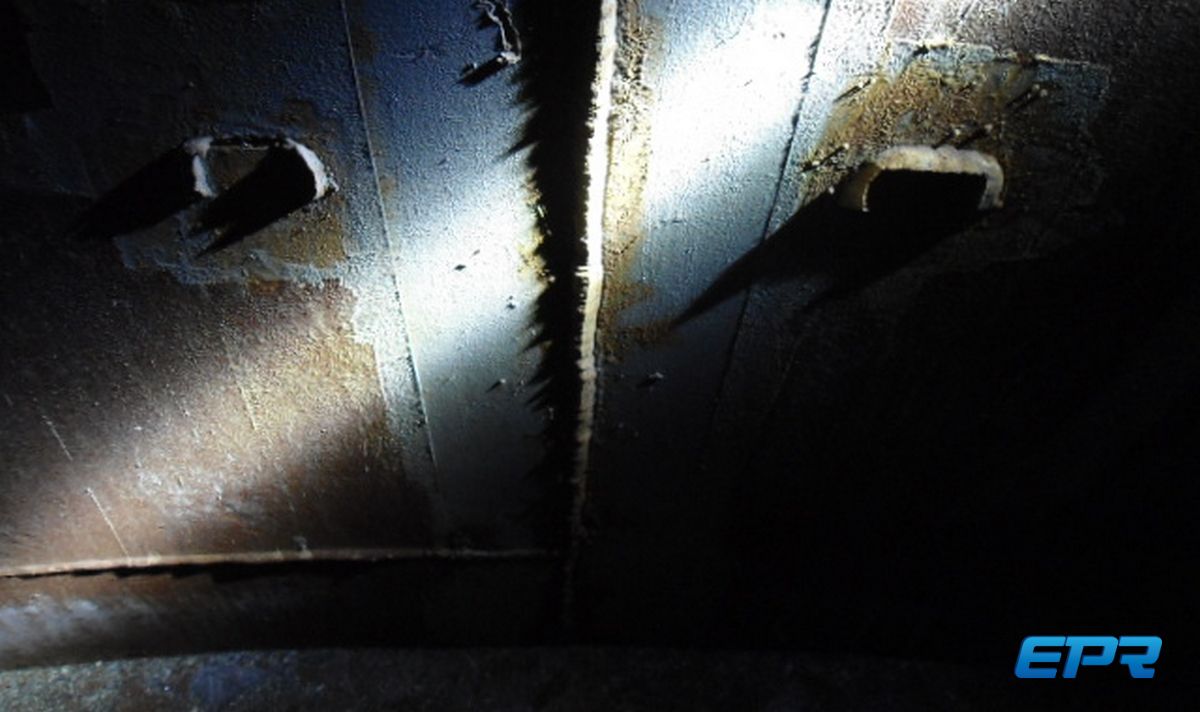
Inspection During Outage
The shadow shows the variety of weld defects prevelant in the stack joint. While AWS D1.1 allows a great deal of latitude in its visual inspection criteria, it doesn't allow this type of "freelancing". Also, notice the alignement lugs which are not ground flush, per specification. No coating would last over such surface imperfections. It is also notable that the "paper" revealed the coatings inspectors approval of the "prep" before the very expensive coating was applied.