Weld Slugs
Proper power plant construction is typically based on layers of processes and checks. Often observed quality problems are concerning due to their possible systematic nature and origin as a supervision problem.
In the realm of field welding, few defects speak as clearly about poor contractor quality and a loss of accountability than a slugged weld. The attached photo reveals that a piece of “all-thread” rod was used to fill several weld passes. Even worse, the welder didn’t even feel compelled to bury the slug under the cap and so it remained exposed. This indicates a site ethic existed, where the welder felt there was no consequence to being caught, or perhaps the welder was confident that no one would verify his work.
There may be several codes or standards that cover this type of activity, but it violates the general welding standards of AWS. The practical reason “slugs” are not acceptable is due to the uncontrolled and usually low-grade nature of the material used as “slugs”. This implies a possible structural deficiency, which is of course not acceptable.
In this facility, there were many examples of this problem. The photos show a few…
The joints need welding, to do it wrong saves no time. Unqualified labor may be marginally cheaper, but not if the work is rejected!
Contractor: Cost of repair is small; but brand damage is meaningful. Owner: Structural failure risk increases, but small. Concerning indicator of plant quality!
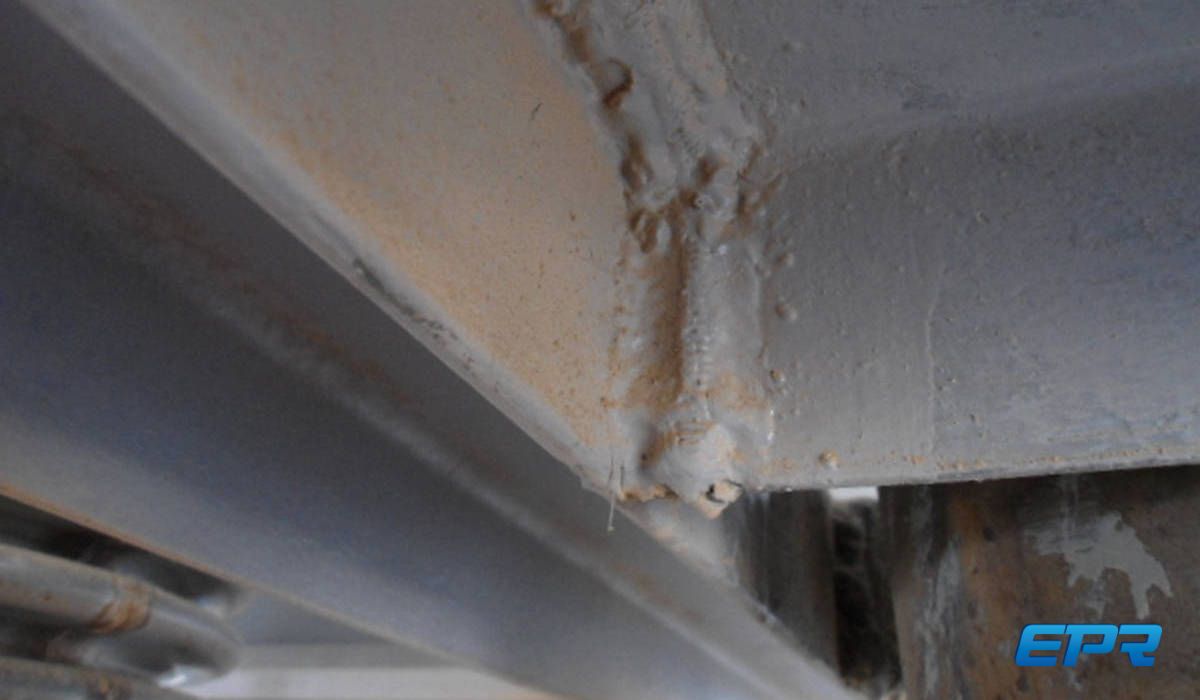
Ugly Twins...
Two slugs in same photo. Aside from the slugs the weld quality is probably not acceptable per AWS D1.1. Overall, just not ideal for a contractor that values their reputation.